Glass wool


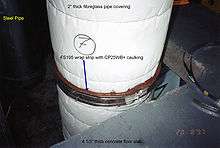
Glass wool is an insulating material made from fibres of glass arranged using a binder into a texture similar to wool. The process traps many small pockets of air between the glass, and these small air pockets result in high thermal insulation properties.
Glass wool is produced in rolls or in slabs, with different thermal and mechanical properties. It may also be produced as a material that can be sprayed or applied in place, on the surface to be insulated.
The modern method for producing glass wool is the invention of Games Slayter working at the Owens-Illinois Glass Co. (Toledo, Ohio). He first applied for a patent for a new process to make glass wool in 1933.[1]
Principles of function
Gases possess good thermal conduction properties compared to liquids and solids, and thus makes a good insulation material if they can be trapped. In order to further augment the effectiveness of a gas (such as air) it may be disrupted into small cells which cannot effectively transfer heat by natural convection. Convection involves a larger bulk flow of gas driven by buoyancy and temperature differences, and it does not work well in small cells where there is little density difference to drive it.
In order to accomplish formation of small gas cells in man-made thermal insulation, glass and polymer materials can be used to trap air in a foam-like structure. The same principle used in glass wool is used in other man-made insulators such as rock wool, styrofoam, wet suit neoprene foam fabrics, and fabrics such as Gore-Tex and polar fleece. The air-trapping property is also the insulation principle used in nature in down feathers, and insulating hair such as natural wool.
Manufacturing process
After the mixture of natural sand and recycled glass at 1,450 °C, the glass that is produced is converted into fibers. It is typically produced in a method similar to making cotton candy, forced through a fine mesh by centripetal force, cooling on contact with the air. The cohesion and mechanical strength of the product is obtained by the presence of a binder that “cements” the fibers together. Ideally, a drop of bonder is placed at each fiber intersection. This fiber mat is then heated to around 200 °C to polymerize the resin and is calendered to give it strength and stability. The final stage involves cutting the wool and packing it in rolls or panels under very high pressure before palletizing the finished product in order to facilitate transport and storage.
Uses
Glass wool is a thermal insulation that consists of intertwined and flexible glass fibers, which causes it to "package" air, resulting in a low density that can be varied through compression and binder content (as noted above, these air cells are the actual insulator). Glass wool can be a loose fill material, blown into attics, or, together with an active binder sprayed on the underside of structures, sheets and panels that can be used to insulate flat surfaces such as cavity wall insulation, ceiling tiles, curtain walls as well as ducting. It is also used to insulate piping and for soundproofing.
Fiberglass batts and blankets
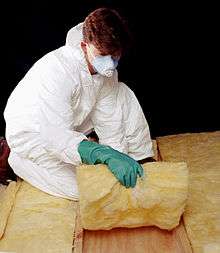
Batts are precut, whereas blankets are available in continuous rolls. Compressing the material reduces its effectiveness. Cutting it to accommodate electrical boxes and other obstructions allows air a free path to cross through the wall cavity. One can install batts in two layers across an unfinished attic floor, perpendicular to each other, for increased effectiveness at preventing heat bridging. Blankets can cover joists and studs as well as the space between them. Batts can be challenging and unpleasant to hang under floors between joists; straps, or staple cloth or wire mesh across joists, can hold it up.
Gaps between batts (bypasses) can become sites of air infiltration or condensation (both of which reduce the effectiveness of the insulation) and requires strict attention during the installation. By the same token careful weatherization and installation of vapour barriers is required to ensure that the batts perform optimally. Air infiltration can be also reduced by adding a layer of cellulose loose-fill on top of the material.
Health problems
Fiberglass will irritate the eyes, skin, and the respiratory system. Potential symptoms include irritation of eyes, skin, nose, throat, dyspnea (breathing difficulty); sore throat, hoarseness and cough.[2] Scientific evidence demonstrates that fiber glass is safe to manufacture, install and use when recommended work practices are followed to reduce temporary mechanical irritation.[3]
In the US, the National Toxicology Program ("NTP"), in June 2011, removed from its Report on Carcinogens all biosoluble glass wool used in home and building insulation and for non-insulation products.[4] Similarly, California's Office of Environmental Health Hazard Assessment ("OEHHA"), in November 2011, published a modification to its Proposition 65 listing to include only "Glass wool fibers (inhalable and biopersistent)."[5] The U.S. NTP and California's OEHHA action means that a cancer warning label for biosoluble fiber glass home and building insulation is no longer required under Federal or California law. All fiber glass wools commonly used for thermal and acoustical insulation were reclassified by the International Agency for Research on Cancer ("IARC") in October 2001 as Not Classifiable as to carcinogenicity to humans (Group 3).[6]
Fiberglass is resistant to mold but often the binder is organic, therefore the binder if organic supports mould growth. In tests glass wool was quite resistant to the growth of mold but at very high relative humidity, 96% or above or if it becomes wet from saturation or indeed liquid water the growth will be moderate.[7][8]
See also
References
- ↑ US Patent Number 2133235: Method & Apparatus for Making Glass Wool First Slayter glass wool patent, 1933.
- ↑ Labor, United States Department of (2005), Occupational Safety & Health Administration, Chemical Sampling Information, CAS Registry Number: 65997-17-3 (Fibrous Glass).
- ↑ North American Insulation Manufacturers Association ("NAIMA"), Insulation Facts #62 "Health and Safety Facts for Fiber Glass", Pub. No. N040, May 2012.
- ↑ Department of Health and Human Services (2011), National Institute of Environmental Health Sciences, National toxicology Program, Fact Sheet, "The Report on Carcinogens," June 2011 (PDF), retrieved 2013-02-05
- ↑ 46-Z California Regulatory Notice Register, P.1878 (November 18, 2011).
- ↑ IARC Press Release, 24 October 2001 (http://www.iarc.fr/en/media-centre/pr/2001/pr137.html)
- ↑ http://www.ncbi.nlm.nih.gov/pmc/articles/PMC1056928/pdf/applmicro00290-0019.pdf
- ↑ Owens Corning (2007), Fiberglass Thermal Batt, Product Data Sheet (PDF), retrieved 2012-02-23
External links
![]() |
Wikimedia Commons has media related to Glass wool. |
- Glass Wool Manufacturers:http://www.glasswoolinsulation.net/
- Glasswool and other Insulation Dealers in Chennai - http://www.natindco.in/